|
|
低溫酸化緩蝕劑 |
Part.1 酸化緩蝕劑的合成與復(fù)配
酸化是碳酸鹽巖油藏開發(fā)過程中油氣井增產(chǎn)、注水井增注的有效技術(shù)措施之一。然而,在生產(chǎn)實踐中,由于酸液對油井的嚴重腐蝕,直至20世紀30年代酸化緩蝕劑問世之后,酸化增產(chǎn)技術(shù)才得以應(yīng)用和發(fā)展。其原理是通過酸液對巖石膠結(jié)物或地層孔隙、裂縫內(nèi)堵塞物等的溶解和溶蝕作用,恢復(fù)和提高地層孔隙和裂縫的滲透率。在酸化施工過程中,通過向酸液中添加緩蝕劑而抑制酸液對井下管柱和設(shè)備的腐蝕。
酸化工藝包括酸洗、基質(zhì)酸化和壓裂酸化。酸化緩蝕劑是酸化施工過程中最重要的添加劑之一,油氣井增產(chǎn)措施使用的所有工業(yè)用酸都需加入緩蝕劑以降低井筒管柱的酸蝕速度。隨著鉆井工藝的發(fā)展和采油技術(shù)的進步,大量深井、超深井和極深井的投入開發(fā),對酸化用緩蝕劑的性能提出了更高的要求。目前酸化緩蝕劑的主流產(chǎn)品是:以酮醛胺縮合物為主劑的復(fù)配體系和以吡啶、喹啉復(fù)合季銨鹽為主劑的復(fù)配體系。 20世紀60-70年代,中國油井較淺(一般在1000-2000m),井下溫度不高(油井溫度不超過80℃),酸化用的鹽酸質(zhì)量分數(shù)不超過15%,一般為10%HCI溶液。該階段主要學(xué)習(xí)前蘇聯(lián),使用甲醛、烏洛托品及亞砷酸(砒霜)等化合物作為酸化緩蝕劑。后來經(jīng)過實驗,證實將兩種以上緩蝕劑復(fù)配制成復(fù)合緩蝕劑往往具有更好的效果,如烏洛托品加碘化鉀、烏洛托品加OP(烷基酚聚氧乙烯醚)、丁炔二醇加碘化鉀、丁炔二醇加OP,丁炔二醇加碘化鉀加OP等。由于該時期油井溫度較低及酸的質(zhì)量分數(shù)不高,使用復(fù)合酸化緩蝕劑,可以使碳鋼腐蝕速率控制在施工允許的條件范圍內(nèi)。 進入20世紀70年代以后,中國石油工業(yè)發(fā)展迅猛,勝利、華北、大港、江漢、遼河及中原等油田相繼勘探成功,一大批二、三千米甚至四、五千米深的生產(chǎn)井投產(chǎn)使用。高濃度大酸量的油井酸化,對酸化緩蝕劑的研究起到了推動作用。70年代末,華中理工大學(xué)與四川石油管理局井下作業(yè)處合作研制出了7701復(fù)合緩蝕劑,解決了油井酸化緩蝕劑技術(shù)難題,在四川第一口6000m(井下溫度196℃)超深井壓裂酸化應(yīng)用獲得成功。之后,高溫酸化緩蝕劑的研究進展較快,7461、7461-102、7801、7812和IMC等一系列高溫酸化緩蝕劑相繼問世,基本滿足了當(dāng)時國內(nèi)酸化施工的需要。 80年代初,不需要復(fù)配甲醛的酸化緩蝕劑被陸續(xù)開發(fā)出來。如四川天然氣研究所研究的CT1-2和CT1-3高溫酸化緩蝕劑可以用在120-190℃的酸化施工環(huán)境中。80年代末90年代初,華中理工大學(xué)鄭家燊等研究出高溫(180℃)濃鹽酸酸化緩蝕劑8601-G(季按鹽復(fù)合物)和150℃鹽酸酸化低點蝕緩蝕劑8401-T及8703-A(季銨鹽化合物),分別在勝利、大慶油田應(yīng)用獲得成功。80年代中后期及90年代,國內(nèi)又一大批油井酸化緩蝕劑研究成功,如CT1-8,IMC-80-5,SD1-3,CFR和XA-139等。 90年代,無機緩蝕劑的研究發(fā)展較快,李德儀推出一批銻化合物作為高溫酸化緩蝕劑及緩蝕增效劑,可供篩選的有Sb2O3,Sb2O5,SbCl3和K4Sb2O7等。陳旭俊研究了抑制鐵基合金孔蝕用的無機緩蝕劑(鉻酸鹽、重鉻酸鹽、亞硝酸鹽、鉬酸鹽及磷酸鹽等)的緩蝕作用機制。 目前國內(nèi)酸化緩蝕劑的主要類型有:醛、酮、胺縮合物;咪唑啉衍生物;吡啶、喹啉季銨鹽;雜多胺;復(fù)合添加增效劑,如甲醛、炔醇等;高分子聚合物。其中,以醛、酮、胺縮合物和吡啶、喹啉季按鹽為主要組成制備的緩蝕劑及其復(fù)配物在生產(chǎn)中應(yīng)用較多。
1.1曼尼希堿型酸化緩蝕劑 曼尼希堿(Mannich base)是指甲醛、胺與含有活潑氫原子的化合物的縮合反應(yīng)產(chǎn)物。曼尼希堿作為緩蝕劑效果較好、發(fā)展前景樂觀,尤其是其在油田酸化作業(yè)中作為高溫濃鹽酸的緩蝕劑而倍受重視. 曼尼席堿的合成方法為:在裝有攪拌器、回流冷凝管和溫度計的三口燒瓶中加入一定量的甲醛(甲醛水溶液、多聚甲醛或能釋放出甲醛的化合物)、含活性氫原子的酮(環(huán)己酮或苯乙酮等)、有機胺(環(huán)己胺或苯胺等),加入一定量的醇為溶劑,加少量酸(鹽酸或醋酸)為催化劑調(diào)節(jié)pH值,加熱在回流溫度下反應(yīng)生成紅棕色的曼尼希堿。下式是以甲醛水溶液、苯胺、苯乙酮為原料,以醋酸為催化劑合成曼尼席堿的反應(yīng)式:
曼尼希堿分子是一個螯合配位體,其多個吸附中心(氧原子和氮原子)向金屬表面提供孤對電子,進入鐵原子雜化的 dsp空軌道,通過配位鍵與鐵發(fā)生絡(luò)合作用,生成具有環(huán)狀結(jié)構(gòu)的螯合物。該化合物吸附在無氧化膜存在的裸露的金屬表面,形成較完整的多分子疏水保護膜,阻止腐蝕產(chǎn)物 Fe3+向溶液中的擴散和溶液中的 H+移向金屬,減緩腐蝕反應(yīng)速度,起到緩蝕作用。 "7801"酸化緩蝕劑的主要成分就是曼尼席堿,作者以苯乙酮、苯胺、六次甲基四胺為主要原料,首先通過六次甲基四胺分解為甲醛和氨,隨后甲醛與苯胺、苯乙酮在催化劑作用下發(fā)生反應(yīng),反應(yīng)結(jié)束后通過減壓蒸餾法分離出未作用完的苯乙酮及苯胺等混合液體,得到棕紅色樹脂狀酮醛胺縮合物,該縮合物的分子量在280左右。通過一系列實驗,發(fā)現(xiàn)反應(yīng)溫度為100℃時,得到的產(chǎn)品緩蝕性能最好。在合成的酮醛胺縮合物中加入丙炔醇、表面活性劑、酒精、六次甲基四胺等混合得到棕紅色的"7801"酸化緩蝕劑,通過掛片實驗證實在28%HCl+2%HAc濃酸液中添加3%"7801"酸化緩蝕劑,150℃時N80試片的腐蝕速度僅25g/m2.h,同時"7801"酸化緩蝕劑具有優(yōu)良的抗硫化氫腐蝕性能。 是另一種以曼尼席堿為主要成分的高溫高濃度鹽酸緩蝕劑,作者先以環(huán)己酮、甲醛、鹽酸為原料,發(fā)生縮合反應(yīng),反應(yīng)結(jié)束后脫水得到中間產(chǎn)物,在中間產(chǎn)物中加入苯胺繼續(xù)反應(yīng)得到酮醛胺縮合物,在合成的酮醛胺縮合物中加入甲酰胺、丙炔醇、非離子表面活性劑及溶劑,混合后得到"CT1-2"酸化緩蝕劑,該酸化緩蝕劑滿足170℃下的濃鹽酸酸化要求。 王虎等以苯乙酮、甲醛及二乙胺為原料,合成了曼尼希堿類緩蝕劑,曼尼席堿的具體合成方法如下:將甲醛、二乙胺和苯乙酮按摩爾比1:1.3:1.3加入三口燒瓶中,再加入一定量的無水乙醇,加熱攪拌回流反應(yīng)10小時,得到棕紅色曼尼希堿緩蝕劑。作者采用電化學(xué)測試技術(shù)研究了該緩蝕劑在20℃、15%鹽酸溶液中對P110鋼緩蝕作用的電化學(xué)機理。極化曲線測試顯示,隨著曼尼席堿濃度的增加,自腐蝕電位向正方向移動,表明曼尼希堿緩蝕劑是以抑制陽極過程為主的緩蝕劑。鄭海洪等研究也證實,較高的緩蝕率是曼尼希堿分子在金屬表面吸附所致,提高緩蝕劑濃度可以增加緩蝕劑在金屬表面的覆蓋度,有效保護金屬基體。 蔣文學(xué)等以芳香酮、醛和芳香胺為原料,用微波輻射法合成了一種曼尼席堿。合成步驟為:在微波反應(yīng)器中加入一定比例的芳香酮、甲醛和芳香胺,加入總質(zhì)量相同量的異丙醇作為反應(yīng)溶劑,并加入一定量的酸調(diào)節(jié)溶液的pH值,利用微波反應(yīng)器合成酮醛胺縮合物。用正交試驗分析法考察了反應(yīng)器的功率、反應(yīng)介質(zhì)pH、反應(yīng)時間、原料比等因素對反應(yīng)的影響,最后得出最佳反應(yīng)條件為微波功率800W、介質(zhì)pH值2、反應(yīng)時間15min、反應(yīng)物料配比(酮:醛:胺)1:2:1,按照上面的反應(yīng)條件得到的產(chǎn)物緩蝕效率最好。
孫天祥等以甲醛、乙二胺、苯乙酮為反應(yīng)主要原料,利用 Mannich 反應(yīng)合成了曼尼希堿緩蝕劑。合成方法:在裝有電動攪拌器、回流冷凝管、溫度計的三口燒瓶中加入一定量的乙二胺,無水乙醇為溶劑,攪拌并滴加鹽酸溶液,調(diào)節(jié)體系 pH 值到反應(yīng)所需的酸度范圍,然后再加入計算好量的甲醛和苯乙酮,不斷攪拌,控制反應(yīng)溫度恒定,持續(xù)反應(yīng)一定時間后,得到均勻透明的棕紅色液體為曼尼希堿酸化緩蝕劑。作者選擇溫度、時間、pH 值、醛酮胺摩爾比作為合成曼尼希堿緩蝕劑的主要影響因素,設(shè)計 4 因素 3 水平的正交實驗,考察合成產(chǎn)物的腐蝕速率,對合成方案進行篩選。實驗發(fā)現(xiàn),在影響產(chǎn)物緩蝕性能的各因素中,反應(yīng)物的原料配比最為顯著,其次是反應(yīng)時間,而反應(yīng)體系的 pH 值影響相對較小。原料配比中,甲醛比例的適當(dāng)增加有利于反應(yīng)的進行。首先醛和胺反應(yīng),生成反應(yīng)的中間體亞甲胺碳正離子,然后再與酮生成具有緩蝕性能的曼尼希堿。苯乙酮分子中的苯環(huán)與 C=O 結(jié)合乙二胺分子中的氮原子,其孤對電子可形成大π健,結(jié)構(gòu)比較穩(wěn)定,因此產(chǎn)物緩蝕效果較好。反應(yīng)過程中,時間太短,反應(yīng)進行不完全,生成的目的產(chǎn)物較少,緩蝕效果不理想; 反應(yīng)時間過長,副反應(yīng)增多,也會影響產(chǎn)物的緩蝕效果。曼尼希反應(yīng)是在弱酸性或中性條件下進行的,需要添加適量鹽酸作為反應(yīng)的催化劑,鹽酸加量不足,反應(yīng)難以進行; 但鹽酸加量過多,也會抑制合成反應(yīng)進行。乙二胺反應(yīng)活性較大,反應(yīng)溫度可以適當(dāng)降低。實驗獲得的最佳合成工藝條件為: 總反應(yīng)時間12h,胺、醛、酮配比為 1: 4 : 2 ( 摩爾比) ,反應(yīng)溫度為 50℃,pH 值控制在 4 左右。用靜態(tài)失重法對其緩蝕性能進行了綜合評價,結(jié)果表明,在 90℃、15% 的鹽酸中加入 1% 的緩蝕劑,N-80 鋼片的腐蝕速率為2.473 g/(m2·h) ,具有良好的緩蝕性能。由酮醛胺縮合物緩蝕機理可知,由于用乙二胺、苯乙酮合成的曼尼希堿分子中含有四個配位原子,能和鐵原子(離子)形成一個五元環(huán)和兩個六元環(huán),生成的螯合物分子以多個極性基團吸附在金屬表面,從而表現(xiàn)出良好的緩蝕性能(圖1.2)。
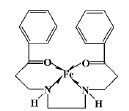
1.2雜環(huán)季銨鹽型緩蝕劑的合成及性能評價 以雜環(huán)季銨鹽類化合物作為主體,得到的酸化緩蝕劑具有優(yōu)良的抗高溫、抗點蝕性能,可廣泛用在鹽酸與土酸的酸化施工中。 雜環(huán)季銨鹽中間體的合成方法為:在裝有攪拌器、回流冷凝管和溫度計的三口燒瓶中加入含氮雜環(huán)化合物(吡啶、烷基吡啶、喹啉、異喹啉、烷基喹啉等)與鹵代物(氯化芐、氯甲基萘等),加熱反應(yīng)生成雜環(huán)季銨鹽中間體。下式是以4-甲基吡啶、氯化芐,合成甲基吡啶季銨鹽的反應(yīng)式:
"7701"酸化緩蝕劑就是一種以季銨鹽為主要成分的緩蝕劑。吡啶釜殘是合成"7701"酸化緩蝕劑主要原料之一,通過吡啶釜殘中的烷基吡啶(4-甲基吡啶,4-正丙基吡啶,2-甲基-5-乙基吡啶,2,4,6-三甲基吡啶等)類和喹啉類物質(zhì)與氯化芐控制溫度在160~180℃范圍內(nèi)進行季銨化反應(yīng),反應(yīng)6小時后,得到中間產(chǎn)物,然后將中間產(chǎn)物降溫至50℃左右并加入勻染劑102和酒精加熱回流后,得到酸化緩蝕劑。"7701"酸化緩蝕劑在室溫時是一種棕黑色油狀液體,在鹽酸或土酸介質(zhì)中有很好的分散性,成清亮透明的棕色液體。通過電化學(xué)研究發(fā)現(xiàn),"7701"在金屬表面上形成的吸附膜可能是多層的,并且"7701"同時抑制了電化學(xué)的陰極和陽極過程,特別是對陰極過程抑制明顯。"7701"與烏絡(luò)托品及丙炔醇等增效劑復(fù)配后得到的"7701"復(fù)合緩蝕劑在150℃、28%鹽酸溶液中對鋼鐵有很好的保護性能,這是由于"7701"與復(fù)合的組分之間發(fā)揮了較好的協(xié)同作用,在金屬表面上發(fā)生了化學(xué)吸附,形成了絡(luò)合體的多層致密的保護膜,阻礙了氫離子與金屬的作用,因而腐蝕速度大大降低。其絡(luò)合吸附膜形成的變化過程是"7701"在鹽酸中離解為芐基吡啶(喹啉)季銨鹽的陽離子和氯離子,而鋼鐵在鹽酸溶液中表面帶負電荷,當(dāng)正電荷的芐基——吡啶(喹啉)的陽離子與金屬表面接觸時,被吸附在金屬表面上,陽離子中的極性基氮原子緊靠金屬表面,非極性烷基及芐基朝向溶液,這樣在金屬表面上好像形成帶正電荷的吸附層,一方面使氫離子難于接近金屬,另一方面,它也可能引起氫超電勢的增加,其結(jié)果就使得鋼鐵在鹽酸中的腐蝕速度大大降低。同時芐基的苯環(huán)上的p電子也增強的緩蝕劑的吸附,因此,"7701"的緩蝕性能較其他苯胺、吡啶單組份好。 宗鵬用氯化芐、二溴乙烷、氯丙烯、環(huán)氧氯丙烷、對氯甲基苯乙烯五種季銨化試劑分別與喹啉和吡啶反應(yīng),合成了12種季銨鹽型緩蝕劑。通過失重法對它們的緩蝕性能進行了評價,并討論了緩蝕劑濃度、酸液溫度、酸液濃度對緩蝕性能的影響,結(jié)果發(fā)現(xiàn):喹啉型季銨鹽的緩蝕劑性能要優(yōu)于吡啶型季銨鹽;六種喹啉型季銨鹽緩蝕性能相比,1,3-二氯化喹啉-2-羥基丙烷<環(huán)氧丙烷基氯化喹啉<1,2-二溴化喹啉乙烷<烯丙基氯化喹啉<(4-乙烯基)-芐基氯化喹啉<芐基氯化喹啉;六種吡啶型季銨鹽緩蝕性能相比,1,2-二溴化吡啶乙烷<1,3-二氯化吡啶-2-羥基丙烷<烯丙基氯化吡啶<環(huán)氧丙烷基氯化吡啶< (4-乙烯基)-芐基氯化吡啶<芐基氯化吡啶;隨緩蝕劑濃度增加,緩蝕效果增強;隨溫度、酸液濃度增加,緩蝕效果減弱。通過Tafel曲線和EIS譜研究了這些緩蝕劑的緩蝕機理,結(jié)果表明:合成的12種季銨鹽型緩蝕劑的緩蝕機理均屬于"負催化效應(yīng)",其中除1,2-二溴化吡啶乙烷是陰極型緩蝕劑外,其余11種均為以抑制陽極反應(yīng)為主的混合型緩蝕劑。用所得機理對緩蝕性能進行解釋,可知:對于季銨鹽型緩蝕劑,緩蝕劑分子的空間位阻越小,分子中能與Fe原子形成配位鍵的基團越多,且形成配位鍵的基團親水性越差,則緩蝕性能越好。 盡管國內(nèi)酸化緩蝕劑的開發(fā)取得了較大的發(fā)展,但是國內(nèi)酸化緩蝕劑的總體水平仍然停留在上世紀80-90年代水平。當(dāng)前,國內(nèi)市場上滿足120℃以下環(huán)境的酸化緩蝕劑很多,但是更高溫度條件下,特別是溫度超過150℃時的成品酸化緩蝕劑產(chǎn)品非常少,而且需要添加較多的碘化物等昂貴的增效劑,導(dǎo)致高溫條件下的緩蝕劑成本很高;變粘酸(轉(zhuǎn)向酸)體系要求酸化緩蝕劑不含甲醛及金屬鹽;作為高溫酸化緩蝕劑的重要組成成分丙炔醇,由于其劇毒性,在很多情況下開始受到限制……,為了適應(yīng)新形勢的需要,還需要開發(fā)出新的、更高效的酸化緩蝕劑。
本文版權(quán)為荊門鑄鼎新材料有限公司(www.shundabxg.com)所有,轉(zhuǎn)載請注明出處
本站關(guān)鍵詞: 酸化緩蝕劑 | 酸洗緩蝕劑 | 二氧化碳緩蝕劑 | 潤濕抑塵劑 | 緩蝕阻垢劑 | 污水緩蝕劑 | 硫化氫緩蝕劑
|
|